Extrusion Coating Lines
- Width of Coating : 500 mm to 5000 mm
- Output Capacity : 50 Kg/Hr to 300 Kg/Hr
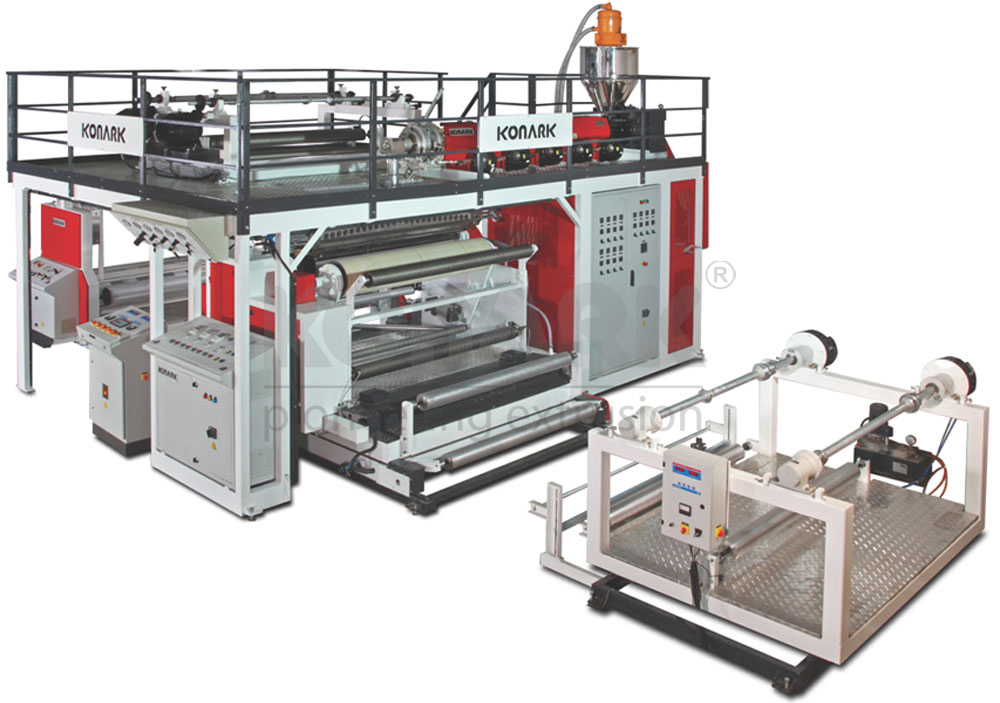
- Wide range of extrusion lines suitable for Woven / Non Woven Fabric Lamination, Paper Lamination & BOPP sandwich lamination with LDPE or PP material
- High productivity with less power consumption
- Coating output starting from 50 Kgs/Hr to upto 300 Kgs/hr
- Smooth Feed type Nitrided Barrels
- Simple or Barrier type Nitrided Screws
- Helical gear box with inbuilt thrust bearing
- Lever type filter changer
- Uniquely designed coat hanger type ‘T’ die ensuring uniform flow distribution
- Unwinder unit with load cell based auto web tension control
- Heavy duty safety chucks with airshafts
- Web aligner unit
- Crease removal banana roller
- Lamination unit forward-reverse & up-down arrangements
- Center type, surface type or turret type rewinding options to suit different requirements
- High density band type and cartridge type heaters
- SSR based all heating zones
- Single point synchronization of whole line with AC motors and AC invertor drives
- Hydraulically operated filter changer
- Turn bar arrangement
- Sandwich lamination
- Corona Treater
- Auto Hopper loader cum dryer
- Water chilling plant
- PP/HDPE Woven Fabric Lamination
- PP Non Woven Fabric Lamination
- Tarpaulin Lamination
- BOPP Sandwich Lamination
- Paper Lamination
- Aluminum Foil Lamination
Tarpaulin Coating Lines ( For Coating Of HDPE Fabric With LDPE Material )
Model | KLM-T/75-2000 | KLM-T/90-2600 | KLM-T/90-3350 | KLM-T/102-3800 |
Material To Be Processed | LDPE | LDPE | LDPE | LDPE |
Screw Dia | 75 mm | 90 mm | 90 mm | 102 mm |
Barrel Feed Type | Smooth Feed | Smooth Feed | Smooth Feed | Smooth Feed |
Maximum Coating Width | 1830 mm ( 6 Feet ) | 2450 mm ( 8 Feet ) | 3000 mm (10 Feet ) | 3660 mm ( 12 Feet ) |
Coating Thickness Range | 20 to 100 micron | 20 to 100 micron | 20 to 100 micron | 20 to 100 micron |
Maximum Coating Output | 110 Kg/Hr | 150 Kg/Hr | 150 Kg/Hr | 250 Kg/Hr |
Die | T – Die | T – Die | T – Die | T – Die |
Winder | Single Station Surface Rewinder | Single Station Surface Rewinder | Two Station Surface Rewinder | Two Station Surface Rewinder |
Machine Connected Load | 90 KW (120 HP) | 118 KW (157 HP) | 122 KW (163 HP) | 195 KW (260 HP) |
Dimensions ( L x W x H ) Apprx |
40 x 30 x 15 Feet | 40 x 30 x 15 Feet | 40 x 30 x 15 Feet | 40 x 30 x 15 Feet |
PP Fabric & Bag Coating Line ( For Coating Of PP Woven & Non Woven Fabric/bag With PP Material)
Model | KLM-TB/90-2000 |
Material To Be Processed | PP |
Screw Dia | 90 mm |
Barrel Feed Type | Smooth Feed |
Maximum Coating Width | 1830 mm ( 6 Feet ) |
Coating Thickness Range | 20 to 100 micron |
Maximum Coating Output | 150 Kg/Hr |
Die | Coat Hanger T – Die |
Winder | Single Station Surface Rewinder |
Machine Connected Load | 106 KW (141 HP) |
Dimensions ( L x W x H ) Apprx |
40 x 20 x 15 Feet |
BOPP Sandwich Lamination Plant
Model | KLM-BP/90-1600 |
Material To Be Processed | PP |
Screw Dia | 90 mm |
Barrel Feed Type | Smooth Feed |
Maximum Coating Width | 1500 mm |
Coating Thickness Range | 20 to 100 micron |
Maximum Coating Output | 110 Kg/Hr |
Die | Coat Hanger T – Die |
Winder | Two Station Surface Rewinder |
Machine Connected Load | 100 KW (133 HP) |
Dimensions ( L x W x H ) Apprx |
40 x 20 x 15 Feet |
Paper Lamination Plants
Model | KLM-PR/75-1100 | KLM-PR/75-1300 | KLM-PR/80-1600 |
Material To Be Processed | LDPE | LDPE | LDPE |
Screw Dia | 75 mm | 75 mm | 80 mm |
Barrel Feed Type | Smooth Feed | Smooth Feed | Smooth Feed |
Maximum Coating Width | 1000 mm | 1200 mm | 1500 mm |
Coating Thickness Range | 12 to 50 micron | 12 to 50 micron | 12 to 50 micron |
Maximum Coating Output | 90 Kg/Hr | 90 Kg/Hr | 120 Kg/Hr |
Die | Coat Hanger T – Die | Coat Hanger T – Die | Coat Hanger T – Die |
Winder | Turret Type Rewinder | Turret Type Rewinder | Turret Type Rewinder |
Machine Connected Load | 86 KW (115 HP) | 90 KW (120 HP) | 120 KW (160 HP) |
Dimensions ( L x W x H ) Apprx |
40 x 20 x 15 Feet | 40 x 20 x 15 Feet | 40 x 20 x 15 Feet |
*All above specifications are just for an idea and subject to change arising out of continuous product change and improvement.